
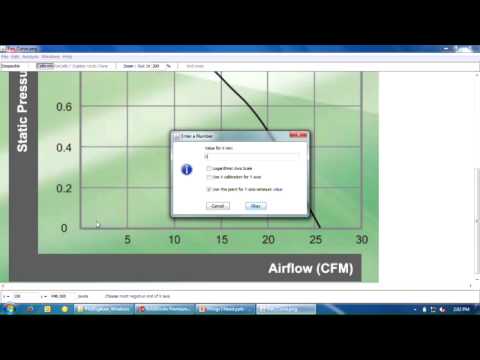
Theoretically, a perfect co-planarity or a perfect tangency should be recognized as a "continuum", but in some cases FloWorks doesn't interprete this correctly (even if SolidWorks' engine does: you can try it by operating a boolean on the tangent bodies). Thomas RE: creating Lids in FloWorks cbrn (Mechanical) 19 Oct 06 02:40ġ- making lids a bit bigger won't puzzle the solver: the recognition of the fluid volume is based upon the SolidWorks' boolean operations and, to make it simple, searches for the number of "solid intersections" and "closed volumes" to find out what is "in" and what is "out". In the Wizard for Result Resolution if the "Manual specification of the gap size " box is ticked for a minimum flow passage of whatever value x.xx m does this have anything to do with lid not Laying on the Boundary between the Solid and the Fluid regions or any Gaps that may exist between the Lid and the Solid ? I tried this making the Lid a little bigger so that it does intersect the Conduit however it works ok with the Ball valve but not my origional Fan Shroud ? Wouldn't this tell the solver that the boundary area is bigger than it should be or is the solver able to figure this out ? com/viewth read.cfm?q id=162141& amp page=1 In another thread that making the lids bigger in order to easily select the Face/Boundary, I basicaly got it all working ok but with mixed results for the lids,(Perhaps a Tutorial about Lids could be explained in some more detail) I changed my Lids and the Model so that there was no longer a radius in the 4 corners of the rectangle, not what I wanted but. 5-11 Creating a Project from the Template. 5-7 Cloning a Project and Creating a New Configuration. 4-18Ĭylinder Drag CoefficientCreating a Project. 4-10 Cloning the Project.4-10 Creating a Cut Plot. 4-8 Running the Calculation.4-9 Monitoring the Calculation. 3-16ĭetermination of Hydraulic LossModel Description. 3-15 Compare the Isotropic and Unidirectional Catalysts. 3-15 Define the Porous Medium - Unidirectional Type. 3-14 Create a Unidirectional Porous Medium. 3-8 Define the Equation Goal.3-10 Solution. 3-4 Create an Isotropic Porous Medium.3-5 Define the Porous Medium - Isotropic Type. 2-27įirst Steps - Porous MediaOpen the SolidWorks Model. 1-23įirst Steps - Conjugate Heat TransferOpen the SolidWorks Model. 1-23 Analyze a Design Variant in the Flow Simulation Application.
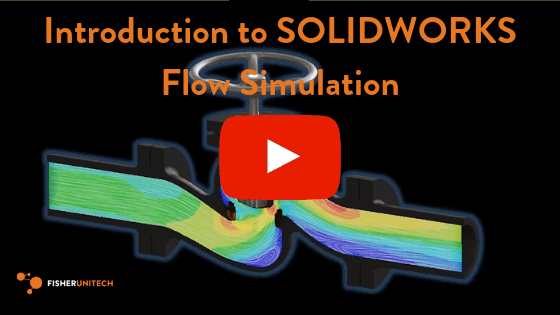
1-19 Analyze a Design Variant in the SolidWorks Ball part. First Steps - Ball Valve DesignOpen the SolidWorks Model.
